Stick Pusher Aircraft - Takeoff distance over 50-ft obstacle | 2,485 ft Rate of climb, sea level | 1,920 fpm Max cruise speed | 290 KTAS Max range, 4 pax 1,803 nm Max operating altitude | 30,000 ft Landing distance over 50-ft obstacle |
2,170 ft The AC646 accident report contains a discrepancy regarding the angle of attack at which the stickpusher of the accident aircraft (a CRJ100, formally a CL-600-2B19, referred to in the aforelinked AAR as a CL-65) would have activated:
Stick Pusher Aircraft

Another innovation is a low, 1,550-rpm propeller setting. Down on the center pedestal is a push-button for shuttling between the electronic propeller governor's normal, 1,700 propeller rpm and a lower, 1,550-rpm mode for a quieter cabin.
Except for takeoff—when the FADEC will automatically command 1,700 rpm—you can use low-speed mode at any time. In cruise, Pilatus says that the penalty is a paltry one to two knots. On final it was autothrottle off, and on short final our VREF airspeed was a mere 76 knots;
with 30 degrees of flaps (maximum is 40 degrees) and reverse thrust we used just 800 feet or so to stop. Unbelievable. Even better, the airplane is easy to land. Just flare slightly and let it settle on the trailing link main gear for a soft touchdown.
The stick shaker is a component of the aircraft's Stall Protection System, which is composed of wing-mounted angle of attack sensors that are connected to an avionics computer. The computer receives input from the AOA sensors and a variety of other flight systems.
When the data indicates an imminent stall condition, the computer actuates both the stick shaker and an auditory alert. The left-hand and right-hand AOA vane angles as recorded on the FDR were compared with the shaker and pusher boundaries adjusted for the phase advance resulting from the rate of increase of aircraft AOA.
This comparison revealed that both AOA vanes reached the shaker trip point, but only the right-hand vane reached the pusher trip point (...) [emphasis mine] Then we got in, went through the pre-start checklists as presented on the ACE's INAV MFD display, and it was a matter of flipping the overhead panel's start switch to get the engine turning.
From there, the job was to monitor the goings-on. Entering the wind and temperature data, then the flight plan came next, then the mandatory check of the stall warning system's stick shaker-pusher system. You bring up the power, then hold the yoke back for three shakes and a push—which wants to yank the yoke out of your hands.
After taking the runway, it's time to arm the autothrottle, bring the PCL up halfway, and let the automation take over. var gaJsHost = (("https:" == document.location.protocol) ? "https://ssl." : "http://www."); document.write(unescape("%3Cscript src='" + gaJsHost + "google-analytics.com/ga.js' type='text/javascript'%3E%3C/script%3E")); try { var pageTracker = _gat._getTracker("UA-8659897-1"); pageTracker._trackPageview(); } catch(err) {} Stick Pusher vs. Stick Shaker On Aircraft var _gaq = _gaq ||

[]; _gaq.push(['_setAccount', 'UA-8659897-1']); _gaq.push(['_trackPageview']); (function() { var ga = document.createElement('script'); ga.type = 'text/javascript'; ga.async = true; ga.src = ('https:' == document.location.protocol ? 'https://ssl' : 'http://www') + '.google-analytics.com/ga.js'; var s = document.getElementsByTagName('script')[0]; s.parentNode.insertBefore(ga, s); })(); var MenuLinkedBy="AllWebMenus [4]",awmMenuName="avstop1",awmBN="778";awmAltUrl="";
awmBuildMenu(); var MenuLinkedBy="AllWebMenus [4]",awmMenuName="avstop2",awmBN="778";awmAltUrl=""; awmBuildMenu(); In the first of the paragraphs quoted, the stickpusher-activation angle of attack is stated as approximately 13.5 degrees (a value which, according to the report, would not have been altered by the aircraft's rapidly-increasing AoA);
however, the very next paragraph implies that the stickpusher would have activated at an AoA of between 8.7 and 9.4 degrees (the right AoA sensor, reading 9.4 degrees, is stated as having reached the stickpusher point, while the left sensor, reading 8.7 degrees,
had not reached the activation threshold by the time the aircraft stalled, thus implying that the threshold AoA for activating the stickpusher was above 8.7 degrees but below 9.4 degrees1), rather than at about 13.5 degrees.
It seems somehow odd that an airplane weighing as much as 10,450 pounds could have a rotation speed that hovers around 75 knots, but the airplane's massive wings and five-blade propeller make it so. With the three of us aboard, we were light at 8,400 pounds but lifted off at 74 knots and went into a 130-knot climb doing 2,300 fpm on our way to FL270.
Using the autothrottle's FMS speed mode, the climb speed then went to 140, then 180 knots as we neared cruise altitude. Up at 270 we set maximum continuous power and burned 414 pph using the 1,700 rpm propeller setting, then 416 pph with the low speed setting.
The true airspeed—282 knots—was identical for each prop setting, but the noise levels were noticeably quieter in the low-speed, 1,550 rpm mode. Information from the flight recorders indicates the following events occurred during the attempted go-around: the stick shaker activated when the aircraft was at 129 knots as the pitch was being increased through 4 degrees;
and the right roll and stall onset occurred and the warbler tone activated when the aircraft was at 124 knots and with the pitch at 9.7 degrees. At the time the warbler sounded, the left and right AOA vane readings were approximately 8.7 degrees and 9.4 degrees, respectively.
The pusher did not activate because, while the right AOA reached its trip point, the left AOA did not. [TSB Aviation Occurrence Report A97H0011, page 8 (page 18 of the PDF), my emphasis.] Next came lunch at the airport's Lincoln Highway Diner, where breakfast is served all day, plus a stop next door to pay the fuel bill at the friendly Trego-Duncan FBO, and then up to FL200 for the return trip.
This time I checked the airplane's envelope protection by entering a 60-degree bank. At 51 degrees, the yoke fights back. It wants to return the airplane to 31 degrees in a measure to prevent the pilot from entering an unusual attitude.
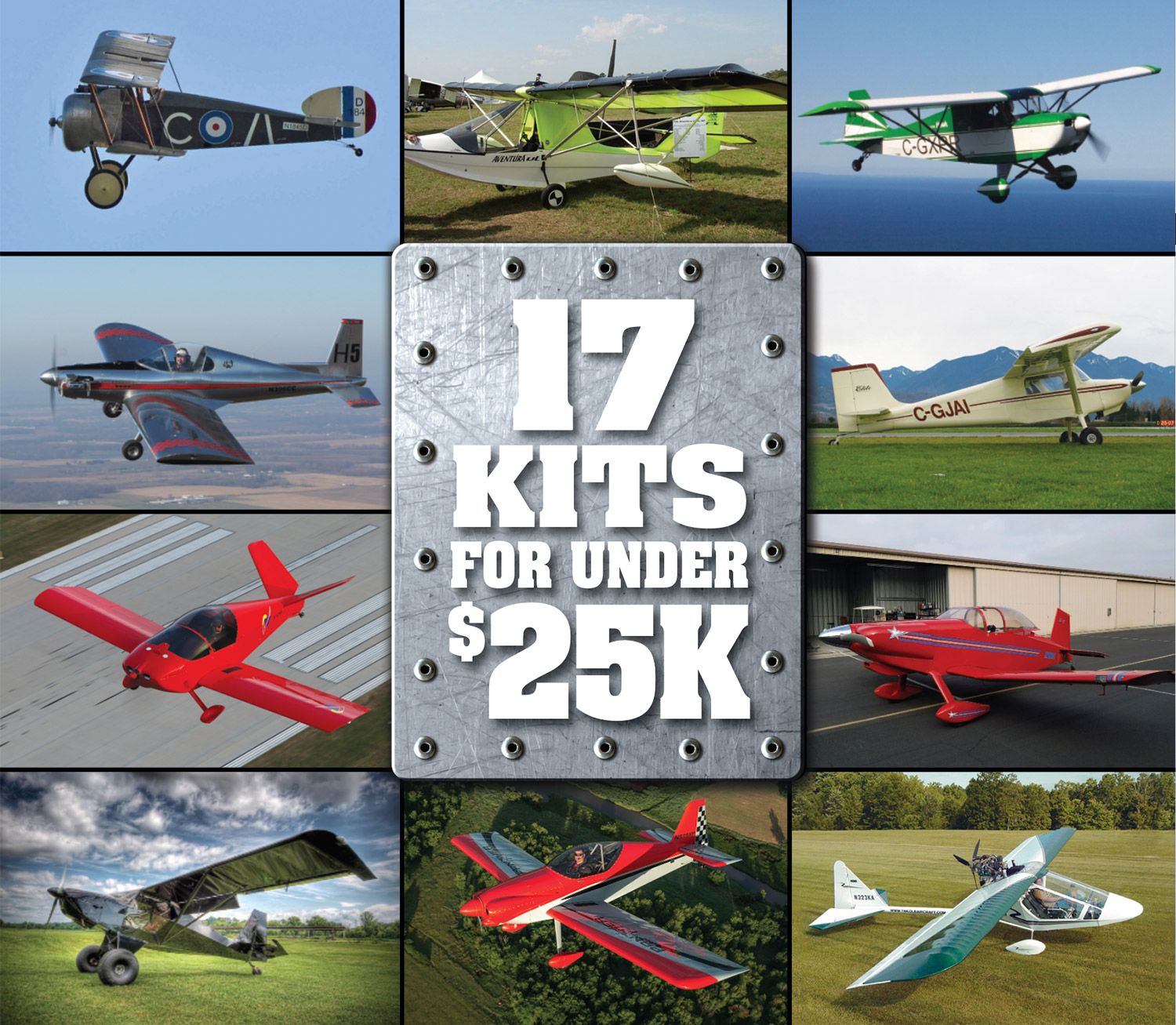
In a recent video (aopa.org/turbine/enginestart), I explained the basic steps in starting a Pratt & Whitney PT6 turboprop engine—similar to the ones in PC-12s and PC-12 NGs. It featured the sequence familiar to many PT6 drivers: checking the battery for adequate power, spooling up to 13 percent Ng, moving the condition lever to low idle, waiting for the lightoff, switching on the generator at 50 percent Ng, and watching out for
an ITT rise that signals a hot start. Well, the PC-12 NGX does away with all that by automating the start with the single flip of a switch. Soon enough, Rocky Mountain's RNAV GPS Runway 30L activated and we started down, finishing up with a VREF of a whopping 82 knots and a pretty nice landing for someone who hasn't been in a PC-12 for five years.
The shaker itself is composed of an electric motor connected to a deliberately unbalanced flywheel. When actuated, the shaker induces a forceful, noisy and entirely unmistakable shaking of the control yoke. This shaking of the control yoke matches the frequency and
amplitude of the stick shaking that occurs due to airflow separation in conventional aircraft as they approach the stall. The stick shaking is intended to act as a backup to the auditory stall alert, in cases where the flight crew
may be distracted. the flaps had retracted a few degrees from 45 and the g was increasing, both of which would cause a slightly higher pusher activation speed; however, there would be no effect on the pusher activation AOA.
[emphasis mine] The NGX cabin is markedly improved from that of its predecessor. To be sure, it retains the split personality (able to handle cargo and/or passengers) and big aft door that so identify the Pilatus brand.
But the new leather seats are taller and narrower, can fully recline, and all have quick-release attach points for turning seating areas into cargo storage; before, only the last two seats were quick release. Thanks to a redesigned seat base there's one inch more headroom, and gone are the old-style storage drawers that opened into the aisle.
Other nice touches include downwash lighting, USB and AC charging outlets, an air conditioning system that puts out more volume of air at less velocity, optional footrests, and—yes—bigger cup holders. Seems the old ones were a tight fit.
A system for this purpose is known as a stick pusher. The safety requirements applicable to fixed-wing aircraft in the transport category, and also to many military aircraft, are very demanding in the area of pre-stall handling qualities and stall
recovery. Digital engine control offers other benefits in the PC-12 NGX. The PCL is linear in its power application, free of any of the flat spots or lags of the sort that can affect fuel control units managed by traditional, manually controlled pushrod linkages.
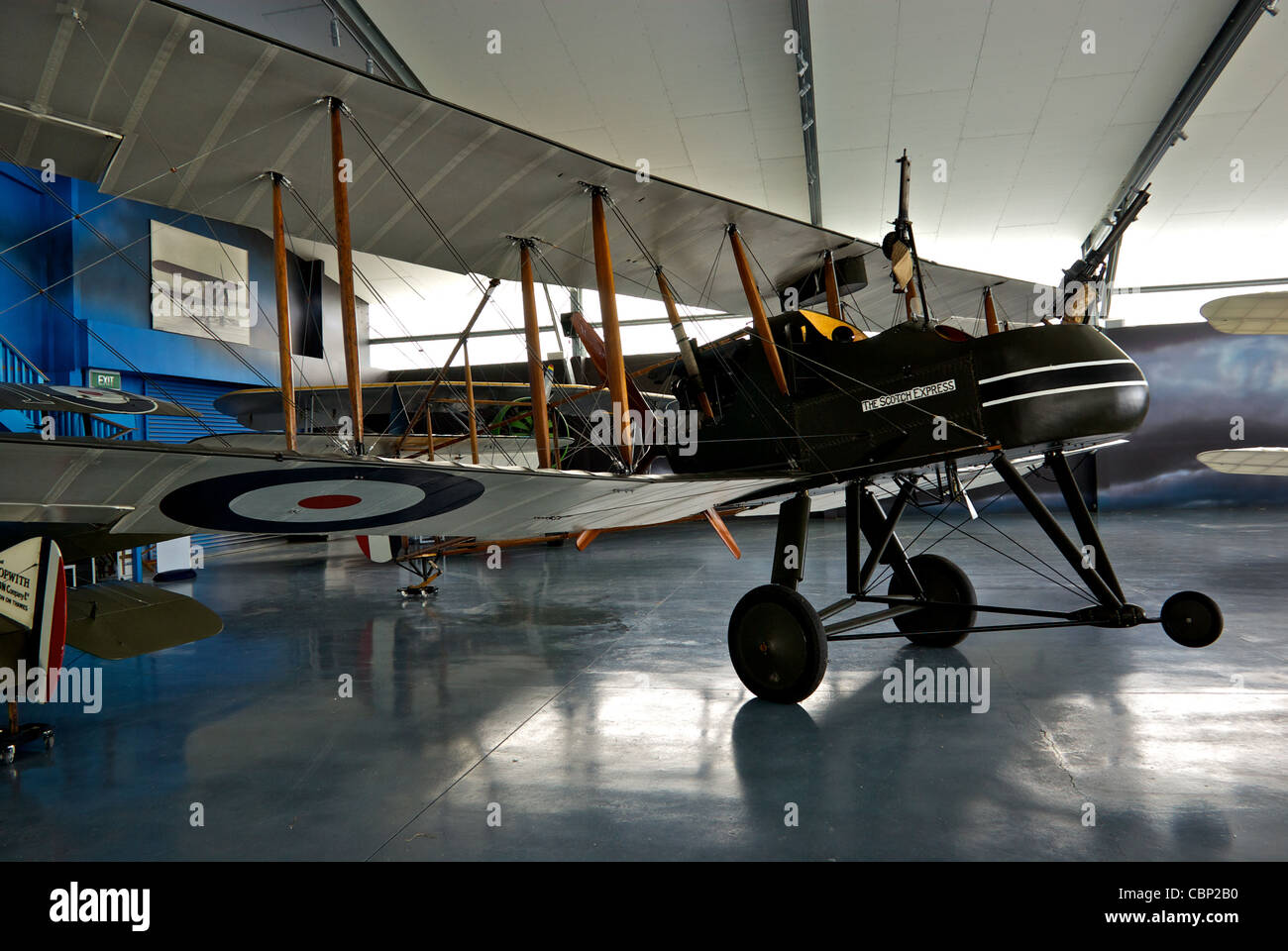
And although the NGX's engine has the same 1,200-shaft-horsepower maximum power output as previous PC-12s, its digital torque limiting function is much more precise, which Pilatus says permits up to 10 percent more thrust in climb and cruise.
This gives the airplane a published maximum cruise speed of 290 knots—five knots faster than earlier PC-12 models. In larger aircraft (especially in T-tailed jets that might be vulnerable to deep stall), some Stall Protection Systems also include a stick pusher system to automatically push forward on the
elevator control, thus reducing the aircraft's angle of attack and preventing the stall. The critical parameters include the angle of attack, airspeed, wing flap setting and load factor. Action by the pilot is not required to recognize the problem or react to it.
Aircraft designers who install stick pushers recognize that there is the risk that a stick pusher may activate erroneously when not required to do so. The designer must make provision for the flight crew to deal with unwanted activation of a stick pusher.
In some aircraft equipped with stick pushers, the stick pusher can be overpowered by the pilot. In other aircraft, the stick pusher system can be manually disabled by the pilot. 1: Due, presumably, to the potentially-catastrophic results of a spurious stickpusher activation at low altitude, the CRJ100/200's2 stickpusher does not activate unless both of the aircraft's angle-of-attack vanes measure an AoA at least as high as
the stickpusher-activation threshold; in contrast, all the automatic high-AoA protections that do not alter the aircraft's flightpath (continuous ignition, stickshaker activation, autopilot disengagement [same threshold as for the stickshaker], stall-warbler activation [same threshold as the stickpusher], and stall-
warning-flashing-light activation [also same threshold as stickpusher]) activate even if just one of the two vanes measures an angle of attack equal to or greater than the requisite threshold. 2: Although the accident aircraft was a CRJ100, the CRJ200 is identical to the CRJ100 except for using a slightly-different variant of the CF34 engine;
the two even share the same CL-600-2B19 classification (making it somewhat difficult, when reading AARs discussing first-generation CRJs, to figure out whether the aircraft being referred to is a CRJ100 or a CRJ200). Power plant |
Pratt & Whitney PT6E-67XP, 1,200 shp Propeller | Hartzell 105-in dia, 5-blade composite, feathering and reversible Length | 47 ft 3 in Height | 14 ft Wingspan | 53 ft 6 in Wing loading | 37.6 lb/sq ft
Seats | 1 + 8-10 Cabin length | 16 ft 11 in Cabin width | 5 ft Cabin height | 4 ft 10 in Cabin volume | 330 cu ft Basic empty weight | 6,173 lbs
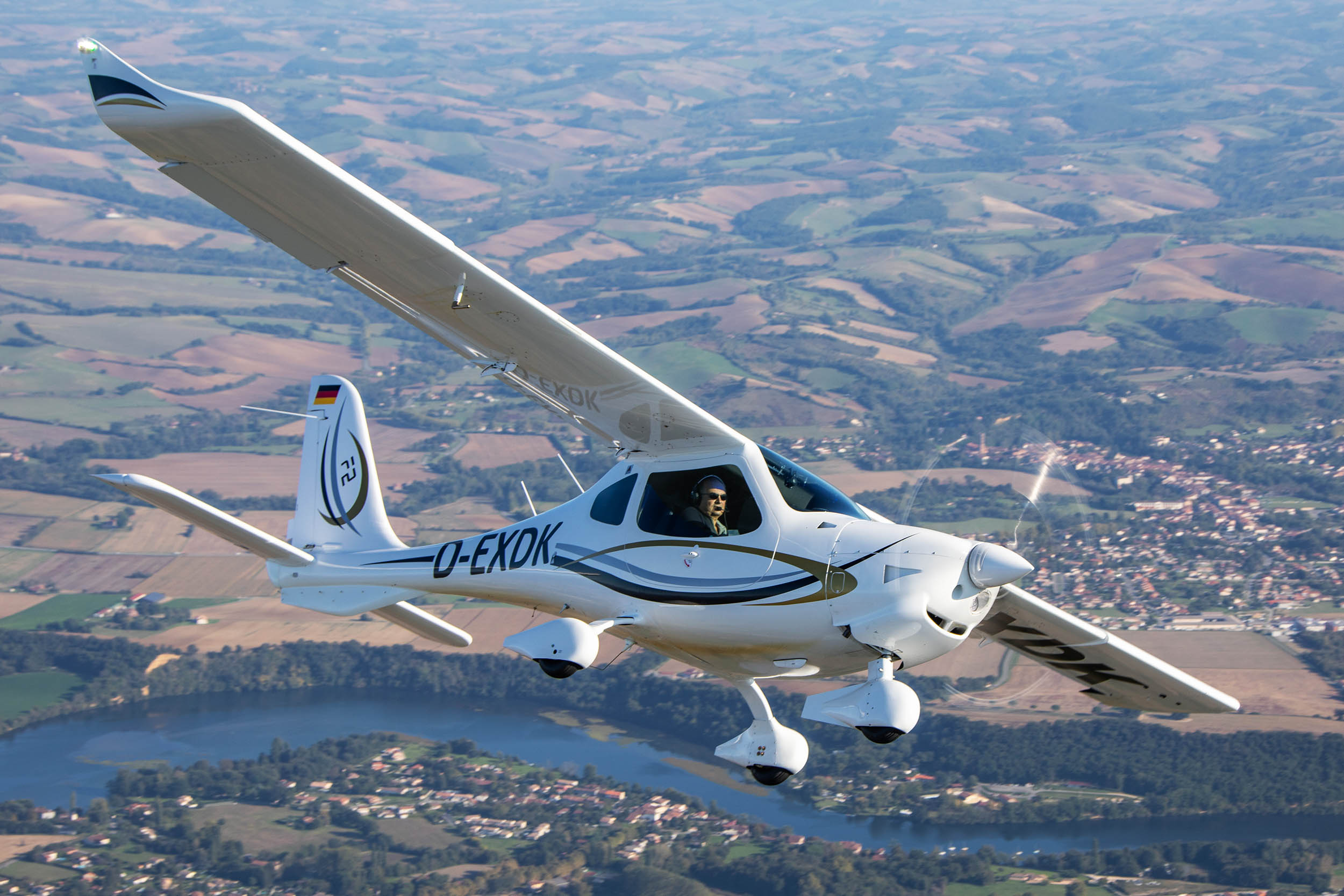
Max ramp weight | 10,495 lbs Max takeoff weight | 10,450 lbs Max zero fuel weight | 9,039 lbs Max useful load | 4,277 lbs Max landing weight | 9,921 lbs Fuel capacity | 406.8 gal (402 gal usable)
Max cargo weight, baggage area | 400 lb, 40 cu ft Cabin | 3,300 lb, 330 cu ft Total sales of PC-12s have hit the 1,700 mark, and all 80 of 2020's PC-12 NGX production positions have sold out.
The marque has found its niche and its place in turboprop history is secure. Some of its signature elements—the airstair door, its ability to fly off of unimproved strips, the large aft door—have become items to emulate among its competitors.
And now, its digital engine controls join them. Soon, it may well be that every new turboprop comes with FADEC. The new engine also has the latest single-crystal compressor blade metallurgy and improved cooling for the power turbine section.
Together with the other enhancements, this gives the PT6E-67XP a 5,000-hour time between overhauls (it was 3,500 hours in earlier PC-12s), and maintenance intervals every 600 hours—twice that of previous PC-12s. In 2008, the PC-12 NG brought Honeywell's Apex glass cockpit to the airplane, among other performance and system upgrades.
The Apex avionics suite replaced the original PC-12's old-school Bendix/King panel, with its round gauges and KLN90B GPS navigator. But the biggest news came in 2019 with the introduction of the latest model: the PC-12 NGX.
The cabin's nice but we all know that the best seats are up in the front office. That goes double for the PC-12 cockpit, with its transport-category seats, generous dimensions, and attention to ergonomic detail. To get a close-up look I went to Pilatus' American headquarters at the Rocky Mountain Metropolitan Airport in Denver, Colorado, and met with Pilatus' chief pilot Jed Johnson and Tom Aniello, vice president of marketing.
Johnson, who with 4,000-plus hours behind the wheel must be the world's highest-time PC-12 pilot, showed off the engine's new fuel system components and the R2-D2-looking electronic propeller control that sits atop the gearbox, fed by a
wiring harness instead of mechanical connections. Changes to the fuel system yield another advantage: Prist, an anti-icing fuel additive, is not required. New, higher-pressure jet pumps and boost pumps in the wing collector fuel tanks now create higher fuel temperatures, and fuel is delivered through smaller-diameter, insulated fuel lines to a fuel filter attached to an engine-mounted fuel control unit.
Before reaching that fuel filter, fuel is warmed by an oil-to-fuel heat exchanger. A fuel temperature gauge on the cockpit multifunction display indicates fuel temperature as it enters the filter. But wait, as the late-night TV ads say, there's more.

The NGX's PT6E-67XP (the "E" is for electronic) also comes with autothrottle. Press the AT button and set a desired airspeed on the glareshield-mounted flight guidance panel, and the autothrottle responds with the power required, whether in climb, cruise, or descent.
Meanwhile, the power control lever (PCL) moves on its own as power requirements rise or fall—as if a ghostly hand were in charge. Looking for a manual override (MOR) or condition lever? Don't bother. The dual-channel FADEC handles those functions as well.
North Platte, Nebraska's Regional Airport was 242 nautical miles away, and with our average speed of 237 knots we arrived in the pattern in 50 minutes. During the descent the autothrottle dialed back the power to maintain our selected airspeed.
Johnson set up the arrival using the visual approach mode, making waypoints defining the downwind, base, and final with 1.5, 1.5, and two-mile legs, respectively. This mode is great for VFR arrivals at unfamiliar airports. The PC–12 NGX retains the PC–12 NG's Honeywell Epic-based glass cockpit platform, but in view of some added elements Pilatus calls the NGX's panel the Advance Cockpit Environment (ACE)—which is also the name Pilatus gave to the avionics suite
in its jet, the PC-24. Yes, for those pining away for a Pratt & Whitney PT6 with a single-lever power control and full-authority digital engine controls (FADEC), the NGX has answered their prayers. The airplane's PT6E-67XP is the launch platform for Pratt & Whitney's first, and long-awaited, foray into the world of turboprop engine automation.
In addition to push-button start, this means that a digital electronic engine control (EEC) unit applies its logic to control and monitor the -67XP. About to have a hot start? The FADEC will automatically shut down the engine.
And for all the other steps in a start sequence, the FADEC handles them as well. There are still other protections—against overtorques, surges, and flameouts, to name a few. If it's above 26 degrees Celsius during shutdown, the engine will motor itself for a few seconds to help it cool down.
A stick shaker is a mechanical device to rapidly and noisily vibrate the control yoke (the "stick") of an aircraft to warn the pilot of an imminent stall. It is connected to the control column of most business jets, airliners and military aircraft.
A stick pusher is a device installed in some fixed-wing aircraft to prevent the aircraft from entering an aerodynamic stall. Some large fixed-wing aircraft display poor post-stall handling characteristics or are vulnerable to deep stall. To prevent
such an aircraft approaching the stall the aircraft designer may install a hydraulic or electro-mechanical device that pushes forward on the elevator control system whenever the aircrafts angle of attack reaches the pre-determined value, and then stops to push when the angle of attack falls
enough.
stick shaker, ac 120 109, airplane stick shaker, airplane pusher, stick shaker in aircraft, aerodynamic stall definition, stick shaker stall warning, undesired aircraft state